Gasket Thickness: A Critical Factor in Sealing Performance
When it comes to keeping leaks at bay, there's one often-overlooked hero that engineers, technicians, and industry professionals need to get just right, with 0% tolerance: gasket thickness. You can't just grab any gasket off the shelf, slap it on, and call it a day. The thickness of your gasket makes or breaks your sealing efficiency, especially in industrial valves, where precision is key. Let's dive into why getting this detail right is crucial.
What is Gasket Thickness and what is its Importance
Gasket thickness isn’t just a trivial number you pick at random, it’s an essential parameter that determines the success of a seal. In industrial applications especially valve applications, the right thickness ensures that the gasket is capable of filling all surface irregularities, withstand internal pressures, and maintain the integrity of the seal over time. Selecting the wrong thickness can lead to disastrous consequences, from leaks to equipment damage. It will compromise the equipment’s performance, safety and longevity.
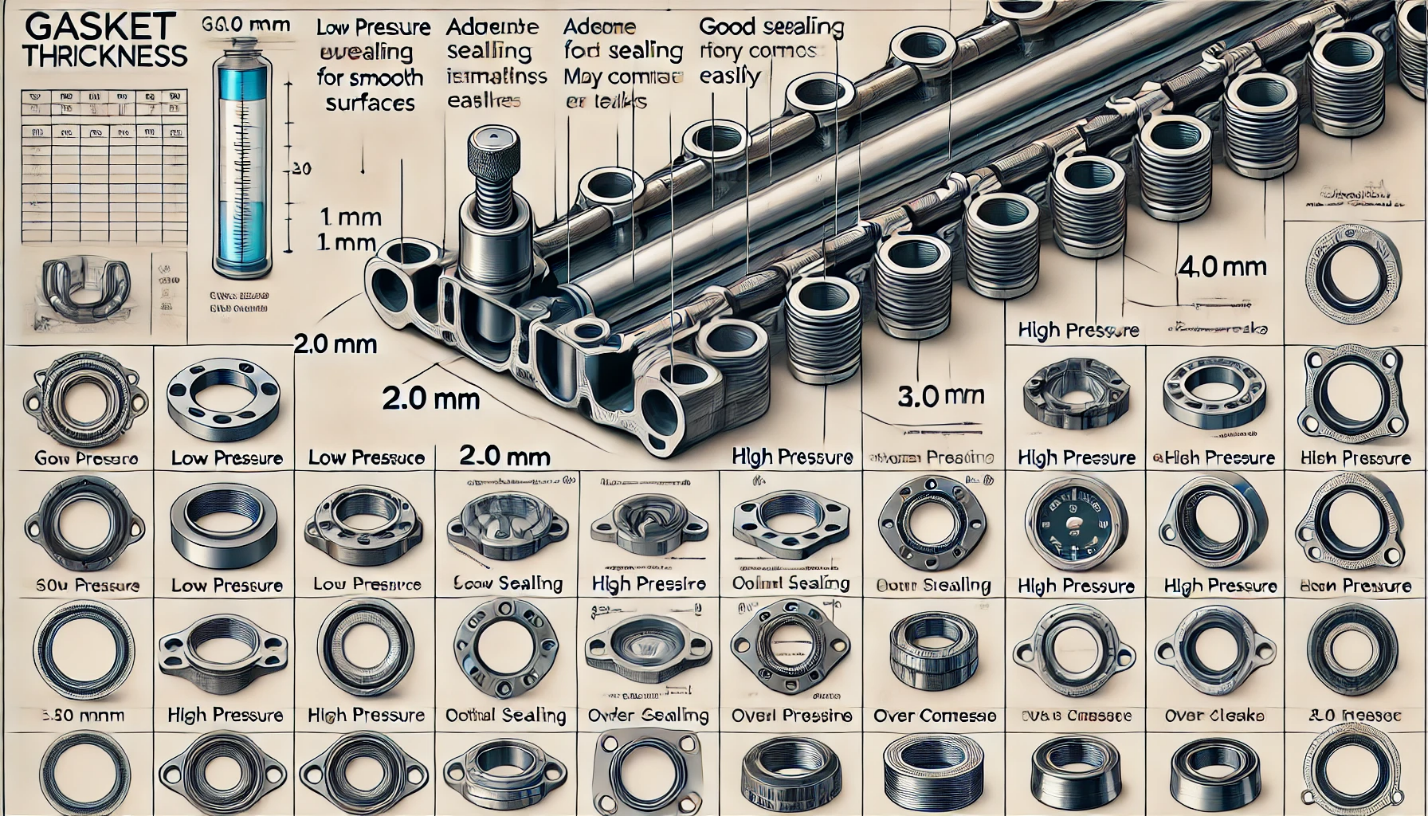
How Gasket Thickness Influences Sealing Performance
The impact of gasket thickness on sealing efficiency is significant. For instance, you can imagine an industrial valve that needs to contain high-pressure steam. If the gasket is too thin, it won't fill the gaps, leaving room for leaks, and you know it can lead to dangerous situations.
On the other hand, if the gasket is too thick, it could be over-compressed, leading to premature failure. Hence the optimal thickness, carefully picked on design calculations will create the perfect amount of contact between the gasket and the flange. It will ensure proper compression and an absolute sealing feature that can keep industrial systems running smoothly.
Comparison of Gasket Thickness vs. Sealing Performance
Let us compare different gasket thicknesses performance for sealing characteristic. The following table will help you understand the performance parameter against Gasket thickness.
Gasket Thickness (mm)
|
Sealing Performance Under Low Pressure
|
Sealing Performance Under High Pressure
|
1.0
|
Adequate sealing for smooth surfaces
|
Insufficient sealing, risk of leaks
|
2.0
|
Good sealing with minor irregularities
|
Moderate sealing may compress easily
|
3.0
|
Excellent for rough surfaces
|
Optimal sealing, risk of over-compression
|
4.0
|
Overly thick, risk of over-compression
|
Suitable for very high-pressure, rough flanges
|
Thickness is Associated with Flange Finish and Flatness
The smoother and flatter the flange surface, the thinner will be the gasket. But there are certain things to know about the finished surface of the flanges and its degree of flatness. Some of the key concepts related to it are:
Surface Irregularities to Decide Gasket Thickness
Flange surfaces are rarely perfect, which is why gasket thickness matters. In industrial equipment like piping and machinery, smoother surfaces allow for thinner gaskets, which provide a firmer seal without unnecessary bulk. Rough or warped flanges, however, need a thicker gasket to fill the imperfections and ensure the valve operates without leakage.
Thinner Gaskets for Smooth Flanges
Smooth flanges often benefit from a thinner gasket, which is enough to compress evenly on the surface to create a reliable seal. For example, in a high-precision industrial valve, a thin gasket can ensure consistent performance without risking over-compression.
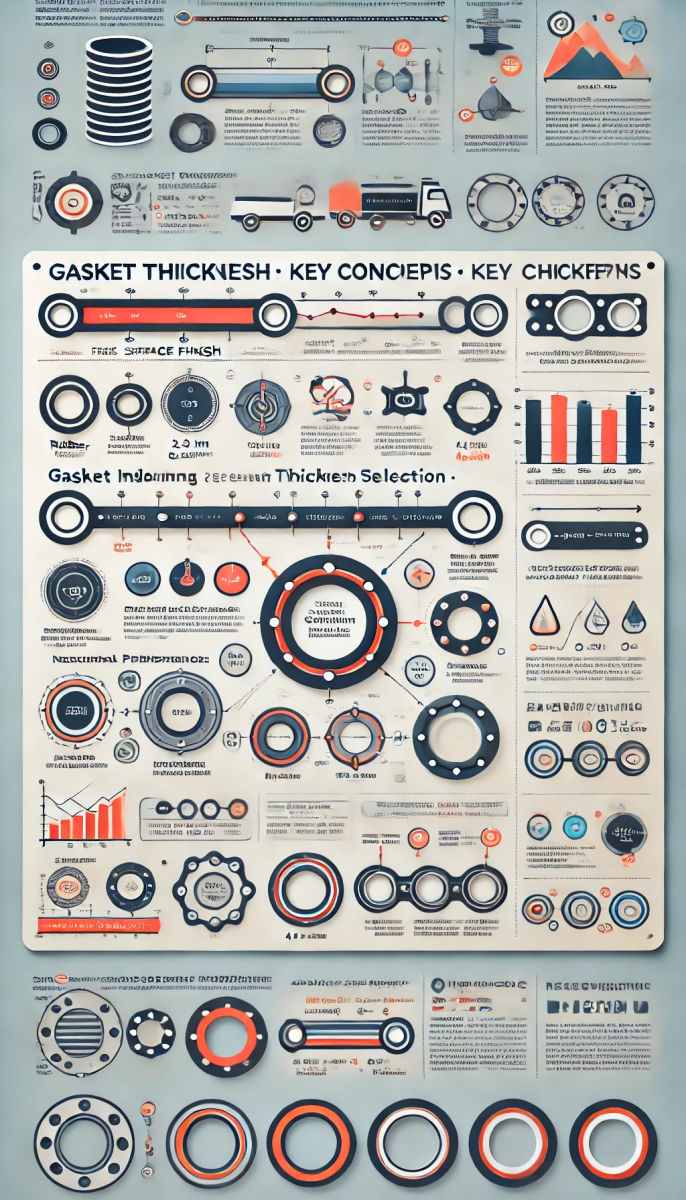
Thicker Gaskets for Irregular Surfaces
For flanges that have seen better days, warped, scratched, or pitted, thicker gaskets can conform to these irregularities better. For example, in older and used valves, where flange surfaces might not be as smooth, a thicker gasket helps maintain seal integrity despite imperfections.
Internal Pressure and Gasket Thickness
The internal pressure that a gasket must withstand directly impacts the choice of thickness. For instance, industrial valves that handle high-pressure fluids require a more robust seal, which often involves a thicker gasket. However, choosing a gasket that is too thick could lead to excessive compression and potential failure, especially under extreme pressure conditions. Balancing gasket thickness with internal pressure is key to ensuring that valves operate safely and effectively.
Temperature Considerations vs Gasket Thickness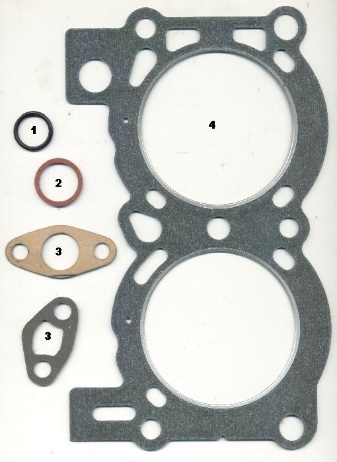
Another factor is temperature. It isn’t something you can ignore when deciding gasket thickness, especially in industrial applications. The valves, machines, equipment and all mechanical products that are exposed to varying temperatures can get their gaskets damaged. These fluctuations can lead to material expansion or contraction, affecting seal integrity.
Gasket Thickness w.r.t. Material Expansion and Contraction
Certain gasket materials expand with heat or contract in cold conditions, which must be accounted for when choosing the thickness. For example, in steam valves, the gasket must be thick enough to accommodate thermal expansion without compromising the seal.
The choice of material is another factor to be learned in detail. In the following section, you will be able to learn about material selection for Gasket.
Gasket Material Selection
Different gasket materials come with their properties, and these influence the ideal thickness for each application.
Compressibility and Recovery
Some materials are more compressible than others, making them suitable for different environments and different thickness requirements. In industrial valves, selecting a material with the right compressibility is crucial for maintaining a reliable seal after repeated use or pressure changes. For example, a PTFE gasket might be chosen for its chemical resistance and ability to recover after compression, making it ideal for certain valve applications.
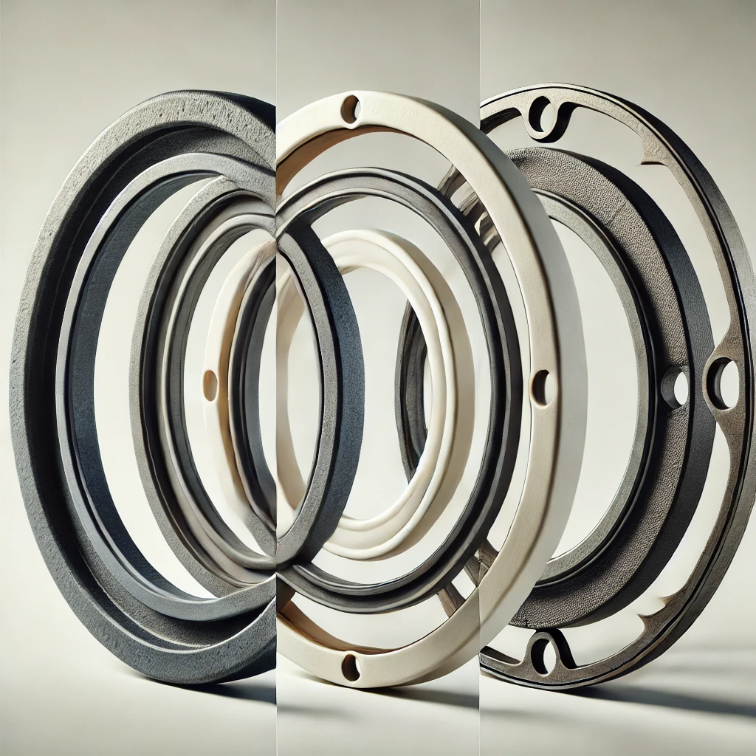
Gasket Material and Recommended Thickness
Gasket Material
|
Recommended Thickness (mm)
|
Suitable Applications
|
Rubber
|
1.5 - 3.0
|
Low-pressure water and air systems
|
PTFE
|
1.0 - 2.5
|
Chemical processing, steam valves
|
Graphite
|
2.0 - 4.0
|
High-temperature and high-pressure systems
|
Metal-Reinforced
|
2.5 - 5.0
|
Extreme pressure and temperature conditions
|
Application and Industry Standards
Specific industry applications have established guidelines and standards dictating the gasket thickness.
For example, ASME B16.21 provides specifications for non-metallic gaskets used in industrial flanges. It offers guidelines for appropriate thickness depending on the type of material and the application. Adhering to these standards ensures that the gaskets meet safety and performance requirements in industrial equipment and valves.
ANSI Standard Chart for Gasket Thickness
ANSI Standard
|
Gasket Material
|
Recommended Thickness (mm)
|
Application Type
|
ANSI B16.20
|
Spiral Wound
|
3.0 - 4.5
|
High-pressure, high-temperature flanges
|
ANSI B16.21
|
Non-metallic
|
1.5 - 3.0
|
Low to moderate-pressure flanges
|
ANSI B31.1
|
Flexible Graphite
|
2.0 - 4.0
|
Power piping applications
|
ANSI B31.3
|
PTFE
|
1.0 - 2.5
|
Chemical process piping
|
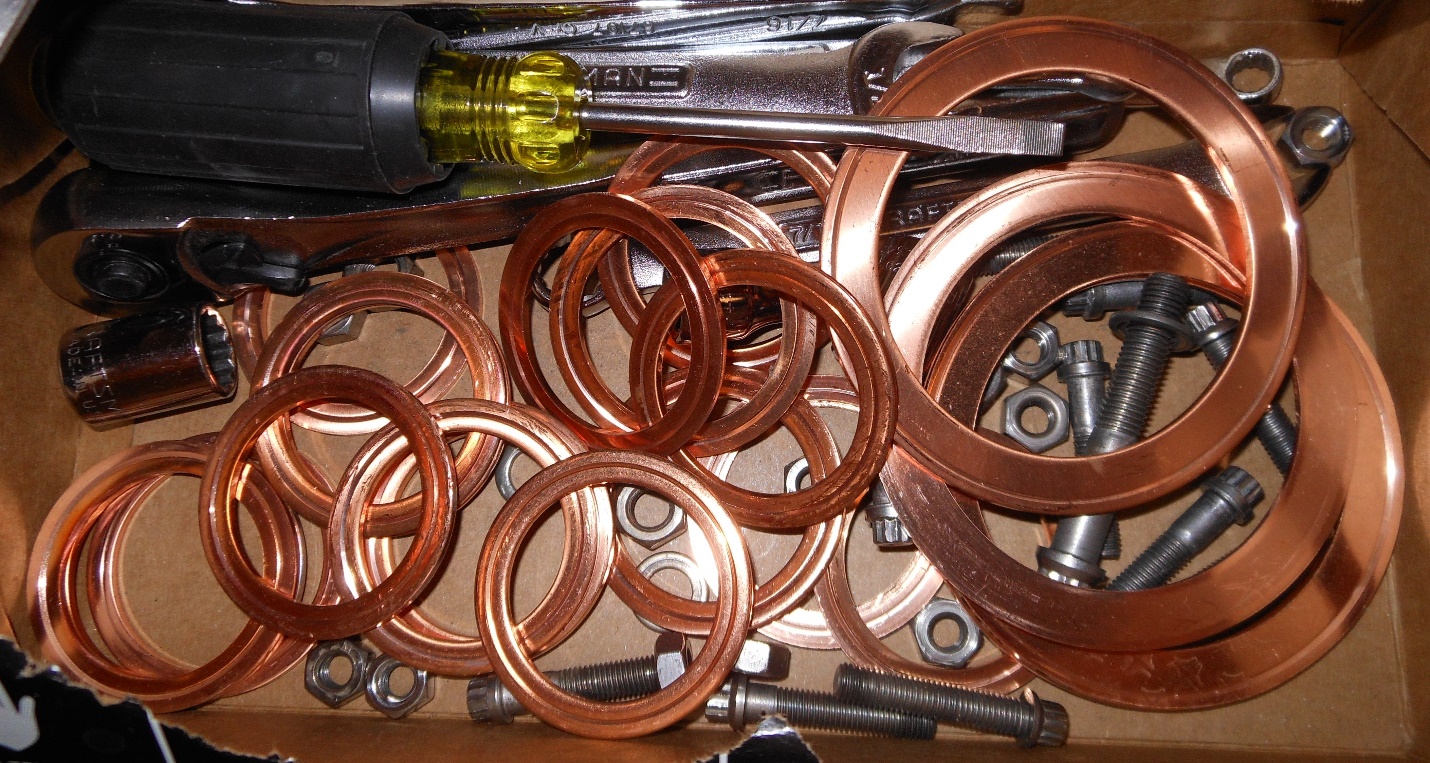
ASME Standard Chart for Gasket Thickness
ASME Standard
|
Gasket Material
|
Recommended Thickness (mm)
|
Application Type
|
ASME B16.21
|
Non-metallic
|
1.5 - 3.0
|
Low to moderate-pressure flanges
|
ASME B16.5
|
Spiral wound
|
3.0 - 4.5
|
High-pressure, high-temperature flanges
|
ASME B16.47
|
Metal-Reinforced
|
4.0 - 6.0
|
Large diameter flanges for extreme conditions
|
ASME B31.3
|
PTFE
|
1.0 - 2.5
|
Chemical process piping
|
Consequences of Incorrect Gasket Thickness
Choosing the wrong gasket thickness isn’t just an inconvenience, it can lead to significant problems, especially in industrial equipment, where the operations stoppage causes significant loss per minute. Some of the issues arising from incorrect gasket thickness are:
Leak Development
The most frequent problem is leakage through the gasket. If the gasket is too thin. It fails to fill the necessary gaps. This allows leaks to develop. For example, in high-pressure valves, this can result in hazardous situations. Similarly, if the Gasket is too thick. The Over-compression can damage the gasket, leading to leaks and reduced valve performance.
Flange Damage
Overly thick gaskets put undue stress on the flanges, leading to potential warping or even cracking sometimes. In industrial applications, this can compromise the entire system, which eventually leads to costly repairs or replacements.
Blowouts
Particularly in high-pressure applications, the incorrect thickness can significantly increase the risk of blowouts. It is an especially dangerous situation in valves controlling critical processes like steam, fuel, fluids and water flow.
Factors Affecting Gasket Performance
We have summarized the critical and most frequently occurring factors that influence sealing efficiency.
Factor
|
Influence on Sealing Efficiency
|
Temperature
|
Affects material expansion and compression
|
Pressure
|
Influences the required thickness for optimal sealing
|
Material Type
|
Determines compressibility and recovery properties
|
Gasket Thickness
|
Impacts the ability to fill surface irregularities
|
Tips for Selecting the Right Gasket Thickness
Now as you have learned the basics of what is Gasket thickness and how it influences sealing efficiency. The question may arise now that there must be a guide to get the gasket of the correct thickness. Although you can hear a lot of suggestions from peer groups, YouTube, the senior management in the industry and people in the supplier market. There are some of the important points that must not be ignored at all.
Consult Manufacturer Guidelines
That is the number 1 tip, ignored by the majority just as policy documents are sent with products. Every gasket manufacturer provides detailed guidelines that specify suitable thicknesses for their products based on the application. For example, for industrial valves, we provide a complete set of calculated instructions, designed by engineers. Following these guidelines helps ensure reliable sealing.
Use Software Tools
Today many tools and handy software applications are available to help you calculate the proper gasket thickness for specific flange types and pressures. You can use these simple tools to find the appropriate thickness, even for equipment and components with complex requirements.
Get Expert Help
If you still are not confirmed, it is normal. It happens with complex requirements such as sometimes the material which will flow through or the pressure variations etc. do not help in determining the gasket thickness. So, when such doubts occur, consult experienced engineers or gasket suppliers who can offer advice based on specific conditions. In industrial valve applications, expert advice can prevent costly mistakes.
For a quick reference, we have compiled a list of FAQs that you can go through in the section below:
Frequently Asked Questions (FAQs)
What is the ideal gasket thickness for optimal sealing?
The ideal gasket thickness depends on several factors, including the type of flange, surface finish, internal pressure, and temperature. Typically, manufacturer guidelines provide recommended thicknesses for specific applications. In industrial valves, the right thickness ensures a proper seal without over-compression.
How does gasket thickness affect sealing performance?
Gasket thickness directly impacts the ability to fill gaps and create a reliable seal. Too thin, and it may not fill surface irregularities, leading to leaks. Too thick, and it could be over-compressed, causing premature gasket failure, especially in high-pressure valves.
Which factors should be considered when selecting gasket thickness?
Key factors include flange surface finish, internal pressure, temperature, and the type of gasket material. For industrial valve applications, it is also important to consider any applicable industry standards or manufacturer recommendations.
What materials are best suited for different gasket thicknesses?
Materials like rubber, PTFE, and graphite are commonly used, each suited to different thicknesses based on their compressibility and recovery properties. For instance, PTFE is ideal for applications requiring chemical resistance, while rubber works well in lower-pressure systems.
How does pressure influence the choice of gasket thickness?
Higher pressure typically requires a thicker gasket to ensure a reliable seal, but excessive thickness can lead to over-compression. In industrial valves, balancing thickness with pressure is crucial to avoid blowouts or flange damage.
Can gasket thickness compensate for surface irregularities?
Yes, thicker gaskets can compensate for irregular flange surfaces by filling gaps that thinner gaskets cannot. This is particularly important in older valves where flanges may be warped or damaged.
What are the common mistakes made when selecting gasket thickness?
Common mistakes include choosing a gasket that is too thin to fill flange gaps or too thick, leading to over-compression. Both scenarios can result in leaks, flange damage, or blowouts, especially in industrial valve systems.
How does temperature affect the gasket thickness required?
Temperature changes can cause gasket materials to expand or contract. In applications like steam valves, the gasket must be chosen to accommodate these fluctuations without compromising the seal.
Final Thoughts
Selecting the right gasket thickness isn’t just a matter of guessing, even if you have 10 years of experience. The metallurgy of both the flanges and gaskets is improving and evolving. It's an engineering science that ensures the efficiency and safety of your equipment. By considering factors like flange finish, internal pressure, temperature, and material selection, you can make informed decisions that enhance sealing performance and avoid costly, dangerous mistakes.